金属、有機材料とともに、工業製品の3大材料のひとつに数えられるセラミック。工業界では、切削・研削用工具、軸受けなどの機械部品、ICや碍子などの電子部品、フェルールやスリーブなどの光通信部品、医療用製品などに、幅広く使用されています。
セラミックは陶器なので、硬い性質を持っていますが、反面、割れやすいという弱点もあります。そこで、セラミックの長所をより強化し、短所を補う加工技術が生み出されていますので、その方法や特徴についてご紹介しましょう。
目次
セラミックとは?
どんな製品に使われているのか
セラミック・金属・プラスチックの性質比較
セラミックの5つの特長とメリットを活かした用途について
セラミックの特長①:熱に強い
セラミックの特長②:硬くて頑丈
セラミックの特長③:電気を通さない
セラミックの特長④:磁気の影響を受けない
セラミックの特長⑤:軽量化できる
セラミックの弱点とデメリットを補う方法について
フカサワのセラミック加工
切削加工
成形加工
抜き加工
まとめ:セラミックは幅広い場所で使われる多彩な素材
セラミックとは?
セラミック(セラミックス)とは、無機物を加熱処理して焼き固めた焼結体で、一般的には陶磁器として認識されています。
セラミックの特徴としては、以下のような点が挙げられます。
- 常温において固体である
- 硬度は高いが、脆く壊れやすい
- 強度、破壊靭性が内部の局所的な欠陥構造に左右されやすい
- 耐熱性に優れるが、熱衝撃によって破壊されやすい
- 金属より軽く、プラスチックより重い
- 絶縁体である
どんな製品に使われているのか
セラミックが使用されている身近な製品や産業製品としては、以下のようなものがあります。 電化製品、自動車から医療の現場まで、セラミックは幅広く使用されています。
- テレビ、パソコンや携帯電話等の基板
- 自動車排気ガス触媒担体
- エンジン等の点火プラグ
- 製鉄用のフィルタ
- 送電線の碍子
- 人工骨、人工歯
- 砥石、研磨剤
- 切削工具の切刃…など
セラミック・金属・プラスチックの性質比較
工業用部品としてよく知られる材料として金属やプラスチックがありますが、セラミックとはどのような特性の違いがあるのでしょう。
金属やプラスチックに対するセラミックの優位点と劣位点を、わかりやすく一覧表にして比較してみました。
金属・プラスチックに対する優位点 | 金属・プラスチックに対する劣位点 |
---|---|
耐熱性 | 脆性 |
耐食性 | 加工性 |
硬度 | 急激な温度変化による破壊性 |
化学的安定性 | – |
絶縁性 | – |
耐薬品性 | – |
耐摩耗性 | – |
寸法安定性 | – |
温度変化による加工性 | – |
金属・プラスチックに比べて、セラミックは熱や腐食・錆への耐性が強く、硬く、化学品や薬品、摩耗にも強く、電気を通しにくい性質であることがわかります。また寸法安定性がありながら、温度変化を加えることによって加工しやすくなるというメリットがあります。
一方で、急激な温度変化や衝撃によって破壊されやすく、そのため、加工しにくいというのが、金属・プラスチックに比べて劣る点であると言えるでしょう。
セラミックの5つの特長とメリットを活かした用途について
セラミックに関する特筆すべき特徴を挙げると、「熱に強い」「硬くて頑丈」「電気を通さない」「磁気の影響を受けない」「軽量化できる」という5ポイントになります。
それぞれの特徴について詳しくご説明しましょう。
セラミックの特長①:熱に強い
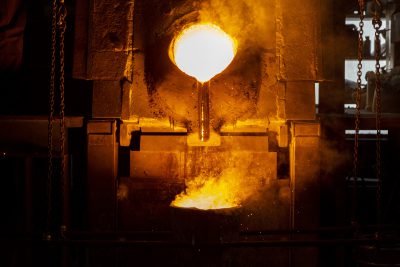
セラミックの特徴として筆頭に挙げられるのが、優れた耐熱性です。セラミックの1種であるアルミナの融点は2,054℃とされていて、鉄(1,535℃)や銅(1,084℃)よりもはるかに高温に耐えられることがわかります。
このハイレベルな耐火性能により、高温環境下での多様な用途に活躍しています。例えば、スペースシャトルの断熱材として、アメリカNASAが採用したのはシリカセラミックのタイルでした。また、溶融金属を入れる容器や、耐火壁などにもセラミックが使用されています。
セラミックの特長②:硬くて頑丈
セラミックは、硬度で耐摩耗性にも優れています。硬さを活かして、研磨剤やカッターとして使用されるほか、摩耗しやすい部品をセラミックに変えることで製品の寿命を延ばせます。
また、セラミックスは粘土や石灰石などの天然素材を原料としますが、人工的な生成方法によりセラミックの特性をさらに強化したニューセラミックス(ファインセラミックス)は、電子、半導体、自動車、産業用機械など、さらに幅広い分野で用いられています。
セラミックの特長③:電気を通さない
セラミックは金属のように電気が流れないため、優れた絶縁体でもあります。この性質を活かし、送電線の碍子(がいし)と呼ばれるセラミック製の覆いが感電を防ぐ重要な役割を果たしてきました。
また、耐久性も高いため、感電防止のコーティング材として用いれば部品の長寿命化に貢献します。温度の変化を監視するためのセンサー、電化製品の過熱を防止するための装置などにも使われています。
セラミックの特長④:磁気の影響を受けない
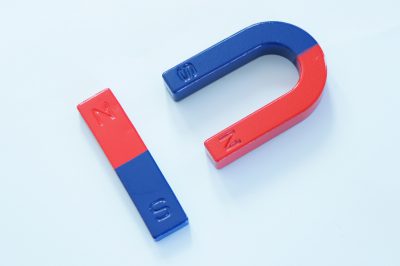
実は、セラミックには磁性を持つものと非磁性のものがあります。磁性セラミックスはフェライトとも呼ばれ、スピーカー、冷蔵庫の磁石、電気モーター、コピー機、レーザープリンター、録音・録画テープなどに多く用いられます。
一方、非磁性セラミックは、磁場と干渉しない部品を必要とする機器の用途に使われています。特にMRI(核磁気共鳴画像装置)などの医療機器、強磁性体検知器、ハイエンドのオーディオアンプなどに重宝されます。また、磁気の影響で金属が使えない場所で重要な役割を果たしています。
セラミックの特長⑤:軽量化できる
セラミックは、ステンレスなどの金属より軽量です。そのため、部品をセラミックに替えることで製品の軽量化が可能になります。自動車産業では、エンジン部品、排気系部品、ブレーキディスクなどに多用されます。
また、軽量化と耐性の両立が可能なことから、ドイツや米国では航空機のエンジン部材に採用されているほか、宇宙関連機器にも応用されています。身近なところでは、片手で持てるスマートフォンにも多くのセラミック部品が用いられています。
セラミックの弱点とデメリットを補う方法について
どんな物質にも長所と短所があるように、セラミックにもデメリットがあります。
セラミックの最大の弱点を挙げるとすれば、それは「脆さ」でしょう。なぜなら、セラミックは原子同士の位置ずれができない結合様式のため、ある程度しなりはしますが、すぐに限界を超えてしまい、変形できずに壊れてしまうからです。
また、セラミックは耐熱性に優れ、種類によっては3,000℃以上の高温にも耐えられますが、急激な温度変化には強いとは言えません。
セラミックに加工を施すことで、こうした弱点や欠点をカバーし、より使いやすく耐久性に優れた部品へとグレードアップすることができます。
フカサワのセラミック加工
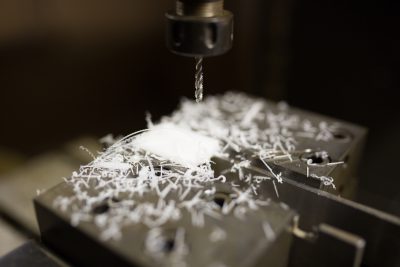
株式会社フカサワでは、幅広い樹脂加工のご要望にお応えしております。ご依頼いただく樹脂部品の中のひとつとしてセラミック部品も含まれており、さまざまな形状・サイズ、品質やロット数、ご予算に合わせて加工を行っております。
当社でお引き受けしているセラミック加工の種類について、ご紹介いたします。もちろん、このほかにもお客様のご要望・ご相談に柔軟に応じております。
切削加工
切削加工とは、その名の通り硬いセラミック素材を切り出したり、削り出したりする加工のことです。他の成形方法と比較すると、切削加工は形状の自由度が高く、複雑な形状の高精度な部品を製造できる加工方法です。また、成形加工と比較して表面の寸法精度を高く仕上げることができ、その分、高い技術力を必要とします。
詳しくは、当社の切削加工ページをご覧ください。
成形加工
ペレット状の樹脂素材を溶かし、金型に押し出して成形する方法で、複雑な形状を高精度で作れるため、多くの小型セラミック部品に用いられています。フカサワでは、以下のような成形加工を承っております。
主な成形加工 | |
---|---|
押出成形 | 加熱して柔らかくなった樹脂を金型から押し出すようにして形を作る方法。 押出成形は、同じ形の製品を大量に作るのに向いている。例えば、セラミックの細い棒状やパイプ状の製品をたくさん作りたい場合、押出成形が効率的。 |
射出成形 | プラスチックの射出成形を応用した技術。セラミック粉末とバインダーを混ぜた材料を加熱し、金型に高圧で注入して成形する。冷却後、バインダーを除去し、高温で焼成することでセラミック製品が完成する。複雑な形状のセラミック製品を大量に、しかも高い精度で作成可能。より高度なセラミック製品の製造が可能で、高品位化、省エネルギー化、薄肉化などの技術進展に応じられる。 |
ブロー成形 | プラスチックのブロー成形を応用した技術で、セラミック粉末とバインダーを混ぜた材料を加熱し、筒状に押し出す。この筒状の材料を金型に置き、空気を吹き込んで膨らませ、形を作り、その後バインダーを除去し、高温で焼成することでセラミック製品が完成する。この方法は、プラスチックのボトルのように、中空のセラミック製品を効率的に生産するのに適している。 |
次に、各成形加工のメリット・デメリットをご紹介します。どの成形加工が良いか、どの成形加工が適切なのか迷う場合、以下を目安のご参考になさってください。もちろん、当社の知識と実績豊富な担当者がお客様のご要望をお聞きし、丁寧にアドバイスいたします。
主な成形加工 | ||
---|---|---|
成形加工の種類 | メリット | デメリット |
射出成形 (単色成形) |
・高精度な複雑形状の成形: 複雑な三次元形状を高い寸法精度で成形できるため、デザインの自由度が非常に高い。 ・大量生産に適している: 金型さえあれば、短時間で大量の製品を均一な品質で生産可能。 ・自動化が容易: 成形プロセスが自動化できるため、人件費削減や品質安定化に繋がる。 |
・材料の乾燥: 樹脂材料の水分含有率が成形品質に大きく影響するため、厳密な乾燥管理が必要。 |
押出成形 |
・形状の自由度が高い: 口金(ダイス)を交換することで、チューブ、パイプ、フィルムなど、様々な形状の製品を製造可能。 ・多様な材料に対応: 熱可塑性樹脂だけでなく、熱硬化性樹脂やゴムなども押出成形が可能。 ・長尺製品の製造に適している: 長尺のチューブやパイプなどの製造に特に優れている。 |
・断面形状が一定: 常に同じ断面の製品しか製造できないため、複雑な形状の製品には不向き。 ・冷却時間がかかる: 製品を冷却する時間がかかるため、生産サイクルが長くなることがある。 |
ブロー成形 |
・中空製品の製造に最適: プラスチックのボトルのように、中空のセラミック製品を効率的に生産するのに適している。 ・生産性が高い: 連続生産が可能で、生産性が非常に高い。 ・軽量な製品が製造できる: 中空構造のため、製品を軽量化できる。 |
・形状の制限: 中空製品に限定され、複雑な形状の製品には不向き。 ・高圧の空気を必要とする: ブロー成形には高圧の空気を必要とするため、設備投資が比較的高い。 |
インサート成形 |
・強度向上: 金属部品を組み込むことで、製品全体の強度や耐久性を向上させられる。特に、負荷がかかる部分や耐衝撃性を要求される製品に有効。 ・機能性の向上: 金属部品の電気的な特性や磁気的な特性を活かし、複雑な機能を持つ製品を製作可能。例えば、コネクタの端子部分や、モーターの固定部分などが挙げられる。 ・部品点数削減: 複数の部品を一体成形できるため、組立工程を簡素化し、コスト削減に繋がる。これにより、生産効率の向上にも貢献できる。 ・寸法精度向上: 一体成形により生産工程を短縮し、生産性を向上させることが可能。例えば、 コネクタ、スイッチ、自動車部品(特に車載用油圧ソレノイド)、医療機器、電化製品などに向いている。 |
・成形条件の調整が難しい: 樹脂と金属の異なる熱膨張率や収縮率を考慮し、最適な成形条件を設定する必要がある。 ・インサート部品の選定が重要: インサート部品の材質、形状、寸法などを適切に選ぶ必要がある。 |
成形加工の詳しい内容は加工の詳細ページをご覧ください。
抜き加工
抜き加工とは、硬い板状のセラミックを型で押し出して、多様な形に切り出す方法です。クッキーの型抜きを想像していただくとわかりやすいかもしれません。高精度な金型が必要ですが、一度金型を作っておけば同じ形の製品を大量に作れます。複雑な形を作るには、高度な技術が必要です。
詳しくは、当社の抜き加工ページをご覧ください。
まとめ:セラミックは幅広い場所で使われる多彩な素材
セラミックは硬度の高さや耐熱性、耐食性など、利点の多い素材で、工業製品はもちろん、陶器から電子機器まで幅広い用途に使われています。ただし、衝撃に対する「脆さ」が欠点で、それを補い、より品質や機能を高めるために加工が施されます。
加工方法には射出成形や押出成形、ブロー成形などがあり、特性を変えるためにさまざまな材料を組み合わせることができます。「こんな形にできる?」「セラミックを使った部品やパーツを加工できる?」といったご相談も大歓迎です。製品の品質向上やコストダウン、生産性の向上など、お客様の課題を解決できるご提案を得意としておりますので、ぜひお気軽に フカサワまでお問い合わせください。